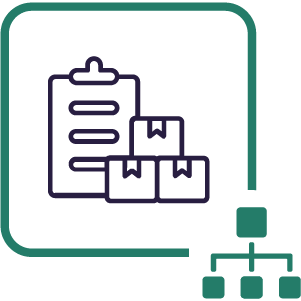
School Inventory Management
Wholeskool enables schools to automate the complex processes of managing inventory.
We understand your challenges. We understand your challenges.
Schools stock a large amount of inventory – whether it’s high-value education technology like computers and interactive whiteboards, costly facilities like AC units and electrical infrastructure, mid-value equipment like classroom furniture and lab supplies, or consumable items ranging from expensive construction materials to simple office stationery.
Keeping track of all these things is not easy. There’s a lot of information to store as new things are acquired, stock is transferred around, and old items are discarded. Constant decisions have to be made. When should an old item be replaced? How do you decide if something is damaged beyond repair? How much should these damaged goods be sold for? Am I acquiring new material at a good rate? Should a new item be bought at all? How do I ensure preventative maintenance is carried out on-schedule and on-quality?
If there is a deficit of skill or trust, or if advanced budgeting is impractical, often senior management or a handful of delegated individuals will be burdened with the responsibility of signing off on these decisions. This over-centralises administration, distracting these people from applying their minds to core education, and relying on the trust placed in a few staff. In practice, this often means that stock is wasted or unaccounted for, and ultimately the school’s money is lost.
We understand your challenges.
Schools stock a large amount of inventory – whether it’s high-value education technology like computers and interactive whiteboards, costly facilities like AC units and electrical infrastructure, mid-value equipment like classroom furniture and lab supplies, or consumable items ranging from expensive construction materials to simple office stationery.
Keeping track of all these things is not easy. There’s a lot of information to store as new things are acquired, stock is transferred around, and old items are discarded. Constant decisions have to be made. When should an old item be replaced? How do you decide if something is damaged beyond repair? How much should these damaged goods be sold for? Am I acquiring new material at a good rate? Should a new item be bought at all? How do I ensure preventative maintenance is carried out on-schedule and on-quality?
If there is a deficit of skill or trust, or if advanced budgeting is impractical, often senior management or a handful of delegated individuals will be burdened with the responsibility of signing off on these decisions. This over-centralises administration, distracting these people from applying their minds to core education, and relying on the trust placed in a few staff. In practice, this often means that stock is wasted or unaccounted for, and ultimately the school’s money is lost.
How can Wholeskool’s School Inventory Management Solution Help?
Wholeskool enables schools to automate the complex processes of managing inventory and stock. This rapidly eliminates the need for direct managerial oversight and human intervention in the life-cycle of physical inventory in your schools.
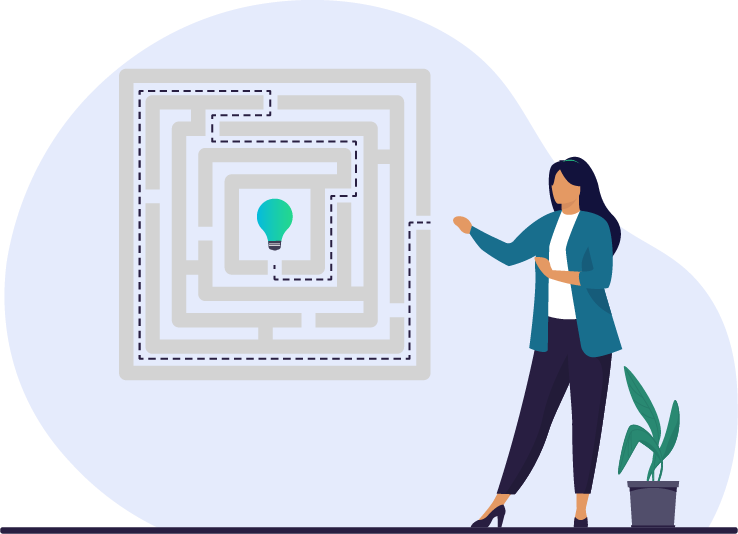
Through a simple one-time setup using Wholeskool’s intuitive policy creation tool, schools can define a set of policies linked to school requirements. This can be done with as much simplicity or complexity as required by the school.
An example of a simple policy would be “The school caretaker should be allowed to order 20 litres of cleaning fluid per 100 square-metres of cleanable floor-area every week”, where the underlined elements are editable as per the school’s requirement. Once this policy is saved, and with information about the floor-areas and other school-specific data pre-entered one time, the system would ensure that no more than the allowed amount is ordered (while allowing an extra order with approval if a special case is justified), without any need for human approvals. The policy could also be set up to allow keeping a constant stock of the material, which is issued as per requirement (within the set limit) and auto-ordered to replenish when stocks are low.
Furthermore, if desired, a weekly or monthly order can be made automatic (so no one would need to actively ‘place an order’), an automatic flag can be raised to the appropriate senior staff in case of under-ordering, or a report by a cleanliness inspector elsewhere in the system could automatically raise a flag to a manger if a fully adequate amount of cleaning material is consistently ordered and yet the place is found dirty, implying that not all the ordered cleaning materials are actually being used properly.
More complex examples might involve using a warehouse, transferring stock between sites or using existing surplus stock on one site to fulfil a requirement on another site, linking allowed quantities of material to other relevant school data (for example, allowing that classroom chairs can be ordered up to the number of students in the school), and much more. Wholeskool can automate this with just some simple one-time policy setup and basic data entry. Relevant data can also be accessed through easy integration with a school’s existing ERP or MIS.
Other features of the module include preventative maintenance of items (for example, ensuring that regular inspections of AC units are carried out); reactive maintenance (for example, resolving tickets raised by individuals who have discovered faulty equipment, with rapid turnaround time); repair, sale, and replacement of damaged items (automating due process to ensure that such claims are only made when genuine and no resources are wasted in the process, while cutting down human intervention); and much more. The module is also integrated with Wholeskool’s Procurement and Construction modules, for seamless ordering of new items whenever required.
In addition, the system allows you to build accountability into it. Ensure that people responsible for resolving maintenance queries do so within a rapid turnaround time, run comprehensive or sample-based stock audits, or impose approval flows (for example, configure the system such that a request has to be checked by a particular hierarchy of approvers, either every time or on a probability-based sample basis).
With Wholeskool, the options are unlimited. With the fully customisable policy rules and process configurations, you can delegate the entire headache of efficient stock and inventory management to the Wholeskool platform. Let the software do the tedious work, so that you and your team don’t have to!